Dodge WC51 A-Frame Crane
By Stephen Carr
Converting the Dodge from a Flying Control truck, back to olive drab was just the first stage of its transformation. Having had something a bit different for so long, I didn't want the Dodge to be completely conventional. I still wanted something that would stand out from other
Dodges; a field-mod conversion that might have been seen on an airfield and something that would be useful too. |
I had dismantled the engine hoist installed in my old garage when we
moved house. I still needed a hoist and brought the steelwork to the new house for possible inclusion in the new garage. I then got thinking of using the smaller section of steel to make a crane in the back of the Dodge, using the existing dolly and chain hoist. It would be something like a No.7 set crane seen in GMC trucks. An initial impression is shown to the right, though the diagonal braces would be mounted inside the bed, with the tailgate open.
The beam out the back and the diagonal braces would be removeable to fit in the garage. To make it safe and secure, there was going to be a lot of metal in there and a lot of weight. It was also going to be a big amount of steel to store if I needed it out of the truck for any reason. Something lighter, quicker to set up and more easily stored would be a better option.
The diagonal braces of the original design were just there to help support the removable beam, but did I really need the beam at all? |
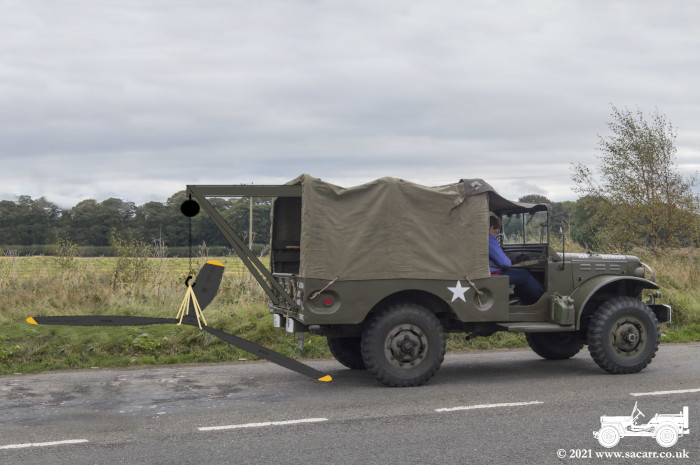 |
The
beam and its supporting structure was going to add most of the weight and complexity. If I made the diagonals an A-Frame crane, it would dramatically cut down on the amount of weight, steelwork and welding needed. Instead of the beam carrying the weight, the A-Frame would carry it, braced by a hand operated wire winch. The winch could raise and lower the A-Frame, giving a longer reach or bringing a load to the point where it could be lifted onto the tailgate/bed of the truck. The chain hoist would still be used, mounted on the end of the A-Frame, to give precise and easy control of any lifting, such as removing a Jeep engine.
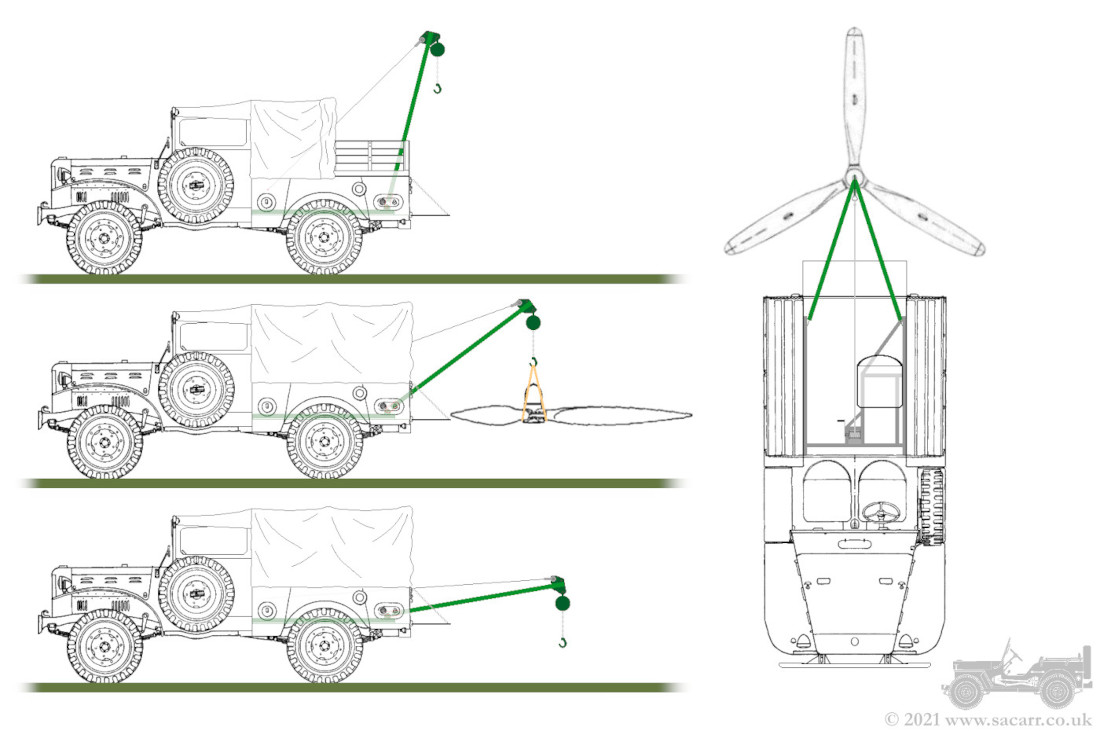
I bought a winch on Ebay to support the A-Frame bars
which was painted as soon as it arrived. The metalwork was ordered
from a local branch of Metal Supermarkets and was cut by the 10th. Once home, I laid out the main A-Frame parts and winch to get a sense of scale. |
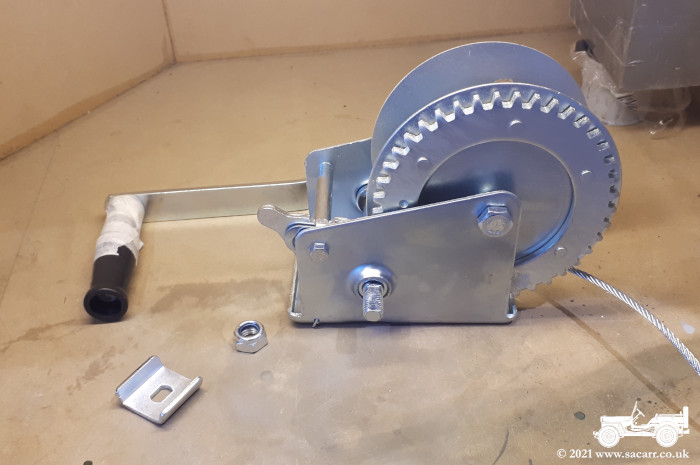 |
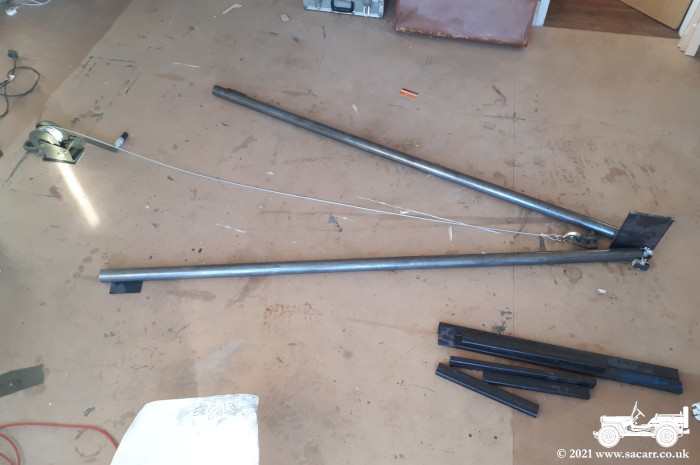 |
On
December 11th, I made a start on removing the framework that supported the child seat and had also supported the
Flying Control observers chair. Some of this structure would be reused.
Below this was the false floor, under which I'd kept my tools and the
spare wheel. It didn't take too long to get it out as it was just held
in with machine screws. Being inside the wooden body of the truck,
they were protected from the weather. The steel angle support frame for the floor was a bit more stubborn, having long bolts from inside the body to the wheel arch. |
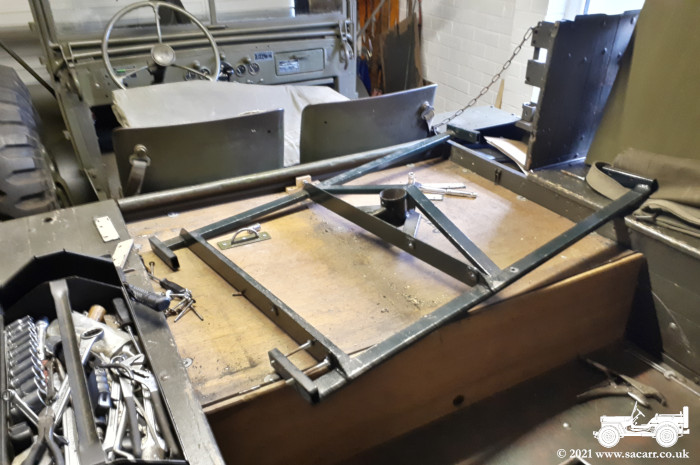 |
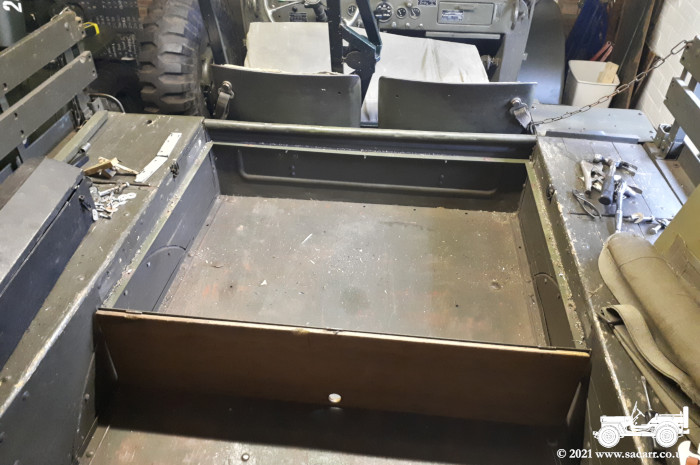 |
The original seat frame
was trial fitted back into the floor of the truck to work out its new
mounting position. My Daughter was called out to check her leg length in the new position and once I was happy that she'd fit, I began to remount the
frame. In addition to holding her seat, it would also be the mount for
the A-Frame winch. The winch position was mocked up with the metalwork
and clamps to establish a height and position where the winch handle
wouldn't hit the floor or front of the truck bed. At the rear of the frame where the seat mounts,
I'd be adding two new vertical mounts to brace the frame from tipping forwards under
braking loads. The rear of the frame would be extended back another 30 inches for the A-Frame mounts, bolted through the bed at the rear. |
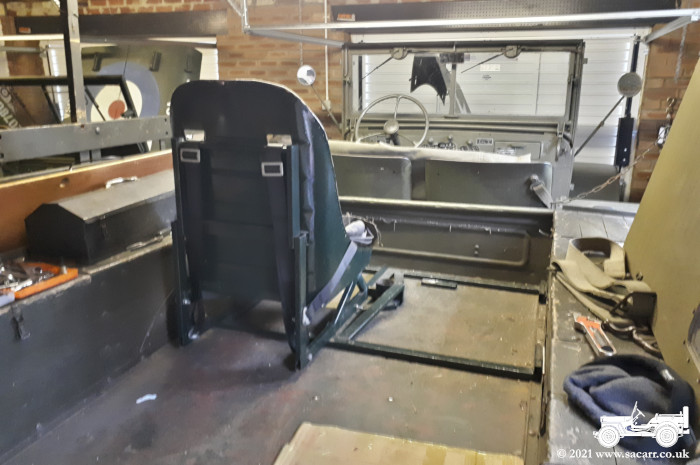 |
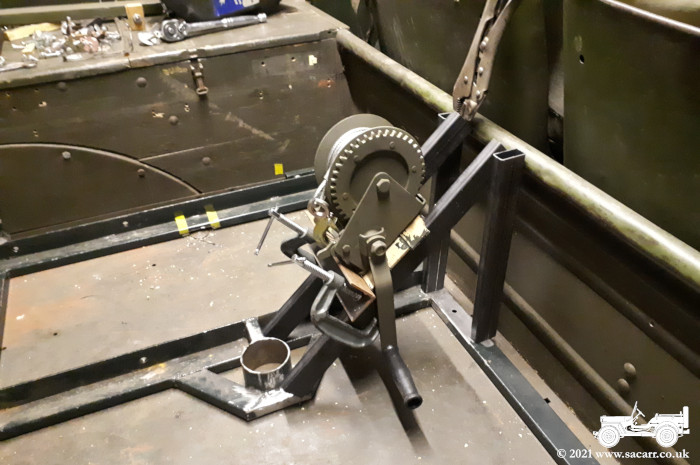 |
The vertical braces for the side of the seat frame were marked up, drilled and bolted in place. The lower end was then welded to the seat frame, followed by cutting a triangle reinforcing piece and welding that in. After that, I moved on to the winch mount. Much of the day was spent cutting, grinding and trial fitting, followed by a few minutes of welding thrown into the
mix.
The diagonals were cut next, which needed lots of fettling to get them to fit the uprights and around the old seat mount at the bottom. The plate for the winch was used to clamp them together to get them parallel for the test fits.
The winch was attached and it was checked for clearance for the handle to rotate without hitting the floor or front face of the truck bed. I also needed to make sure there was hand/knuckle clearance!! Once I was happy the the position, it was tacked in place and the winch checked
again! |
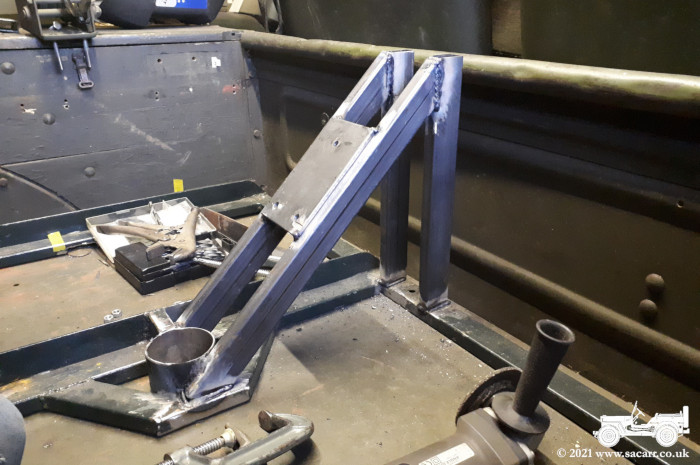 |
With the winch in place, I wanted to check its position in relation to the child seat. I'd removed it to make more space in the truck, but lifted it back out from under the truck for a temporary fit check. There was enough space for my daughter to climb in passed the winch and it also allowed me to check the winch cable would clear the seat. |
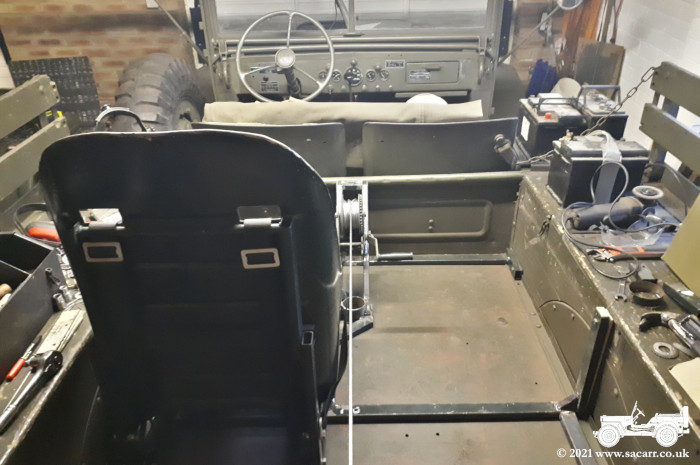 |
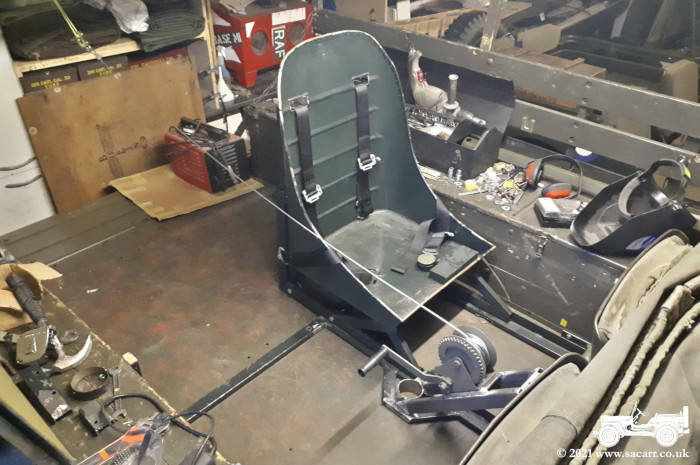 |
For
the next stage, I needed to turn the Dodge around in the garage, so the tailgate is at the garage door end.
I'd then be able to open the garage door and jig up the A-Frame bars sticking out of the door.
This would allow me to work out the hinge angles and to trim the mating faces of the bars where the chain hoist mounting plates
would attach.
On Tuesday
December 14th, I started the A-Frame head, the flat plates that both the winch cable and chain hoist attach to, on the end of the round bars. A 1/1 scale drawing was made first to check how the hoist would hang in relation to the hole, plate and bar at various angles. The angles and hole centres were marked up with tape next, then drilled for a joining bolt. This will be used for holding the two sections of the A-Frame together when complete. Another bolt hole was drilled in an area that will be cut off. This bolt is just to hold the two plates together while being cut and shaped. With the two bits bolted firmly together, centre holes were drilled for the winch cable attachment and chain hoist hook.
Since I don't have a 20mm drill bit, or a hole cutter, or a pillar drill big enough to handle
them for that matter, the large holes would be opened up by chain drilling. Wooden templates were epoxied over the centre holes as a guide for the chain drilling. They would also help to hold cooling oil in the area while drilling. It took some time with a 4mm bit to chain drill both holes, after which the plates were separated and the webs between the holes broken through to release the waste from the centre of the holes.
|
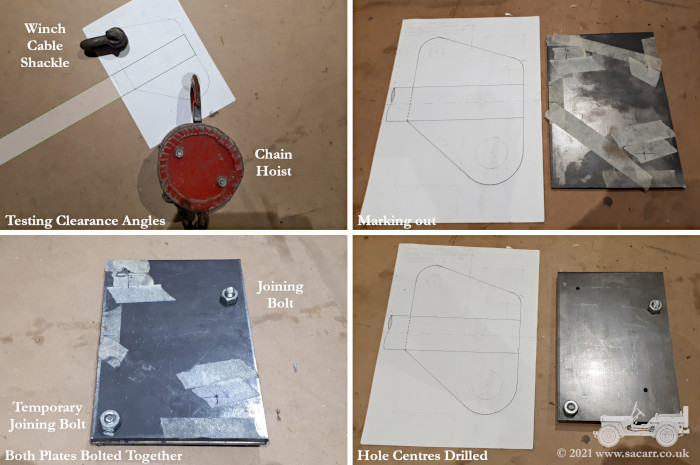 |
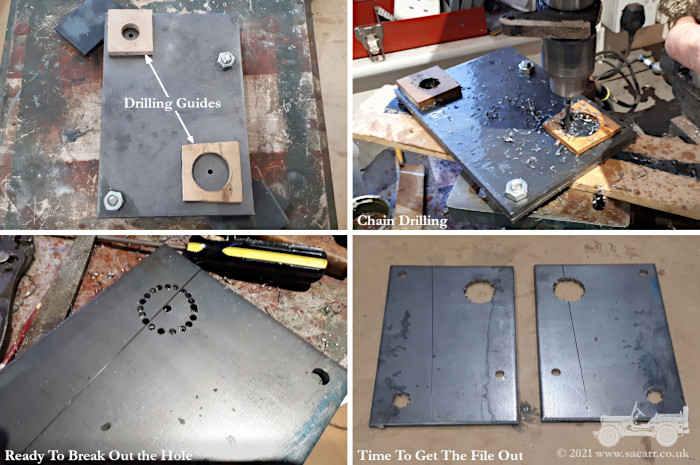 |
The chain hoist was partially dismantled
and both the case and hook given a coat of olive drab. The main hoist needs to dry before turning and the other side
painting. The following day, they were given another coat of olive,
along with the cable winch. |
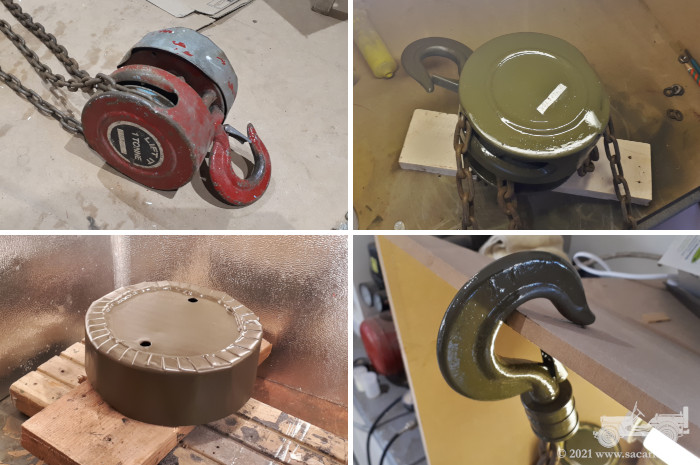 |
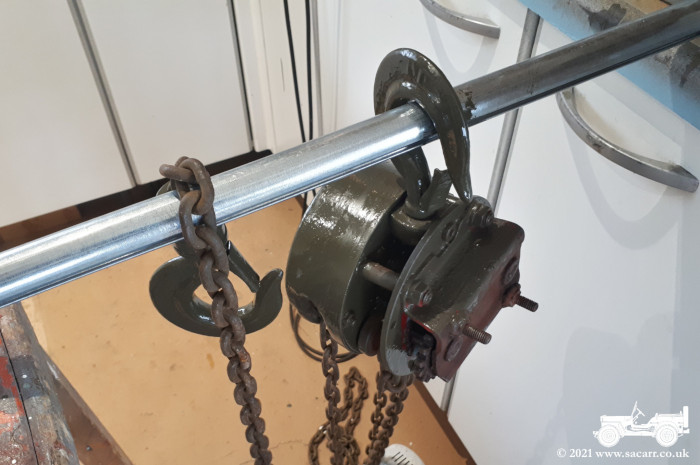 |
It was a hard day of elbow grease on the 15th. With the holes rough cut the day before, it was time to get the files out to clean up the edges of the holes. The larger hole took most of the morning using a combination of a half round file to take most of the material off and a power file to finish. The smaller hole was too small for my half round file, so I started off with a smaller round file. Again, it was slow progress until I spotted a conical grinding wheel in the bits box next to my lathe. This was fitted to my pillar drill and was spot on for the hole size I wanted. It took around an hour, working from each side of the combined 1/2 inch thick steel plates. I found it worked better with a little oil to both lubricate the stone to stop it jamming and to create a cutting paste from the debris it was removing. |
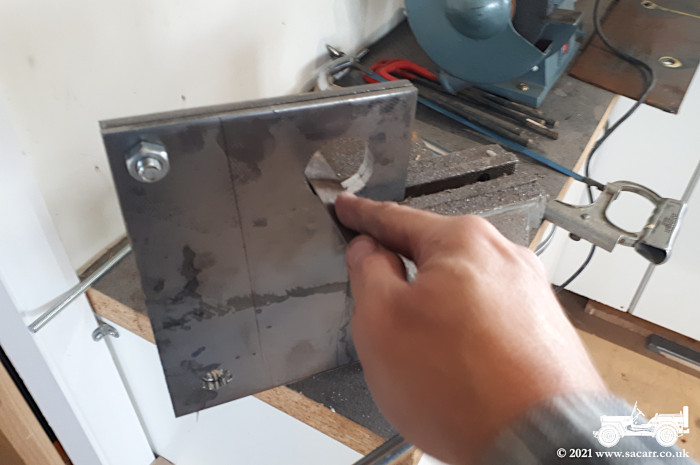 |
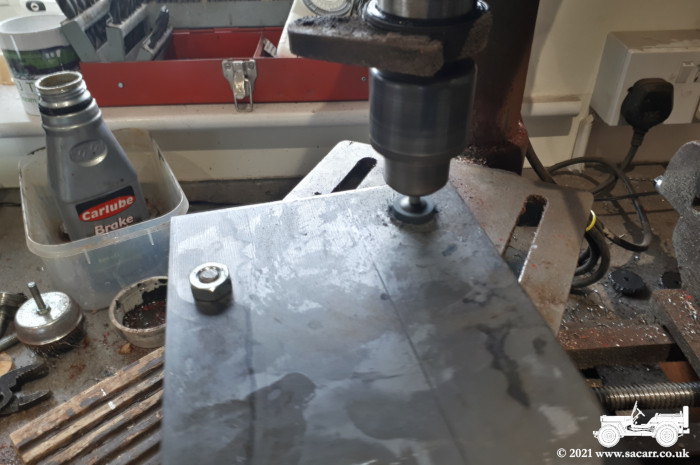 |
With both holes cut, it was time to start trimming the plates. I don't have any huge metal shears and with 1/2 inch of steel to cut through, the angle grinder was the only option I had. The top angle and rounding off by the shackle hole was cut first. The bottom corner was still being used to bolt the two plates together. The 1/2 inch thick steel put up a good fight, but eventually, the top was cut free. All the other corners were rounded off next and lastly the bottom angle. I cut from both ends, all the way through, leaving a small section in the middle holding everything together and aligned until the last minute when the corner was finally broken free. |
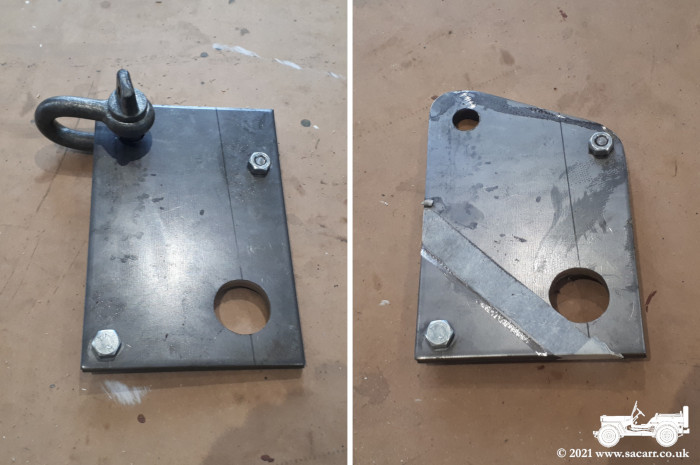 |
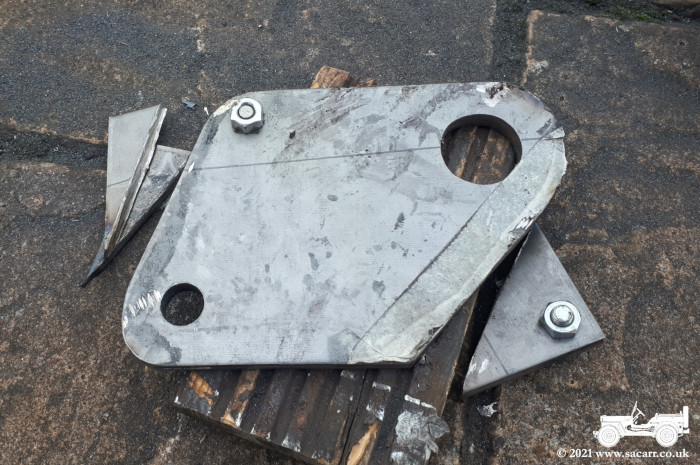 |
I wanted to join the winch hook to the A-Frame head via a 'U' shackle. However, the shackle was to thick to clear the safety jaw on the hook. I didn't want to reduce the diameter of the shackle, so modifying the hook as the only option. The end of the spring loaded jaw was cut off, allowing it to open back away from the hook. This of course meant it would no longer stay closed, but it would open outwards to let the shackle into the hook. A new
stainless steel tip was added to the safety jaw, pivoting on a small bolt. The end of this tip was formed into a 'V' shape so that it would seat into the inside shape of the hook with the original spring keeping pressure on it which held it in place. |
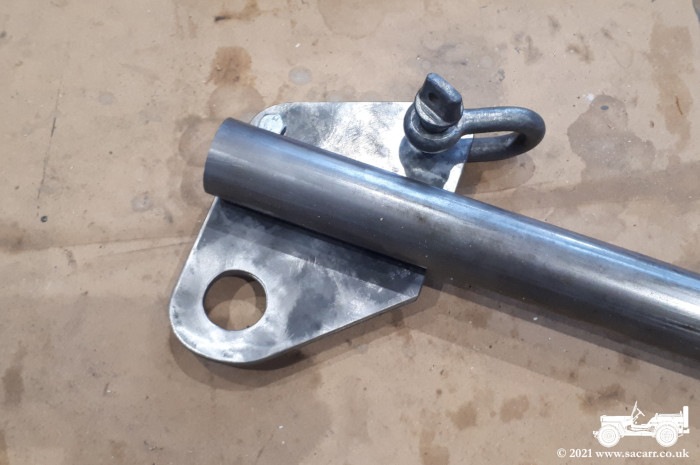 |
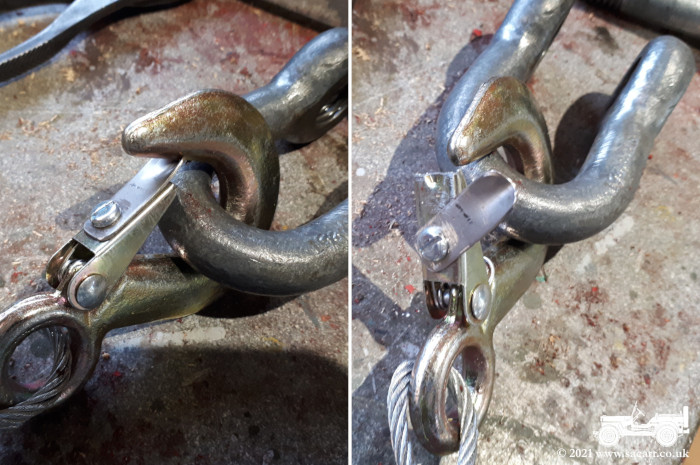 |
The Dodge was turned around on the 16th, allowing easy access to the back of the truck and more space with the garage door open. While I was out there, I balanced the bars on a stool, along with the crane head, to get a feel for the scale of the
crane before going any further. I could always extend the A-Frame bars
with additional tubes if I wanted it longer. At present, the 2 metre
bars are a compromise on being big enough to be useful and not too big
to store. |
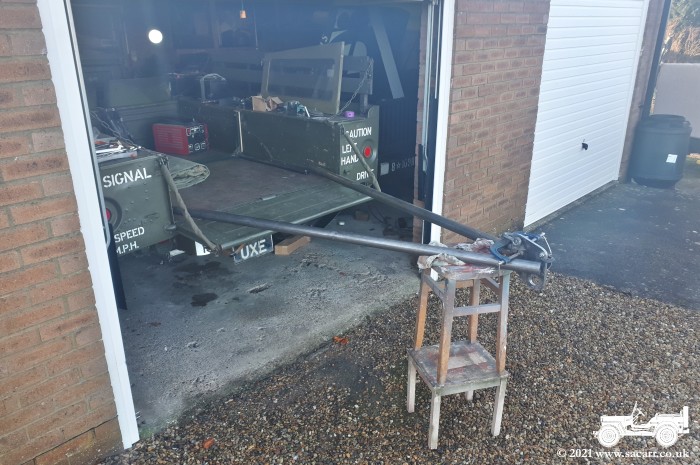 |
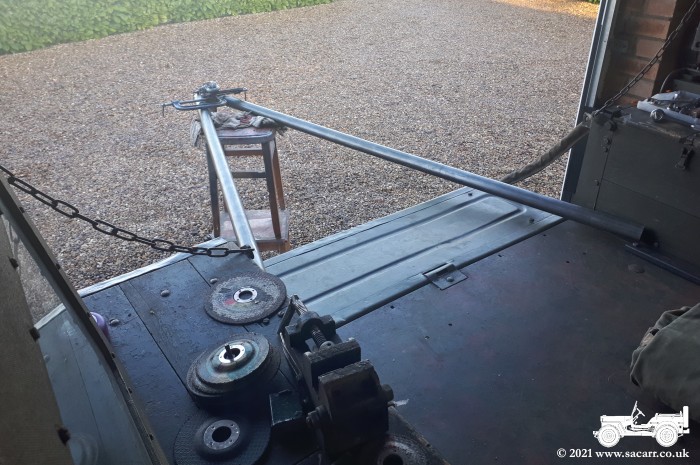 |
I began the 17th in the workshop, drilling the hinge plates for the bars and floor frame. The bars were then taken onto the patio and one end slotted for the hinge plate with an angle grinder. Out to the garage next and the hinge mounts were jigged up on the floor frame using some studding to hold the position and spacing. They were then given a few small tack welds to hold them in place in case I needed to make any changes. |
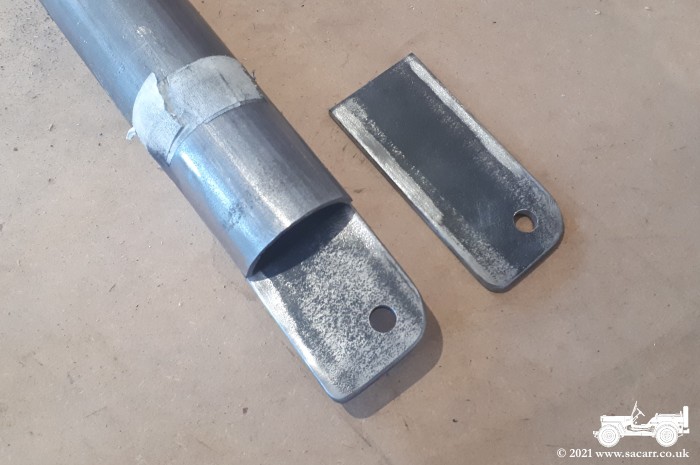 |
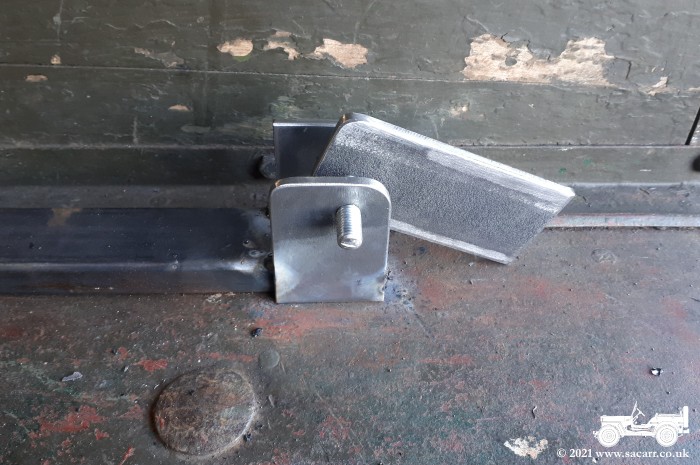 |
After a quick check that the hinge plates were clear of the bolt holding the floor frame to the floor, the hinge plates were welded into the A-Frame bars. This allowed them to be temporarily mounted to the hinge mounts with some studding. With the bars fitted in the truck bed, the top ends were pulled together to work out the taper angle that they would need to be cut to, in order to fit the frame head. The cut lines were marked with masking
tape. More noise and sparks from the angle grinder got them cut, followed by more noise as the faces were fine tuned to fit together with the crane head between them. |
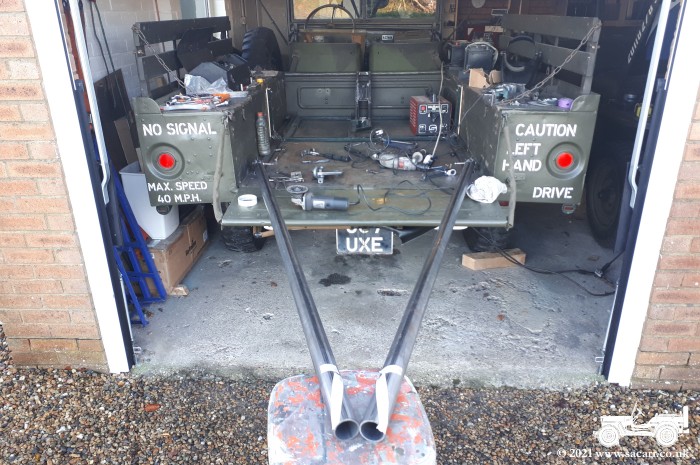 |
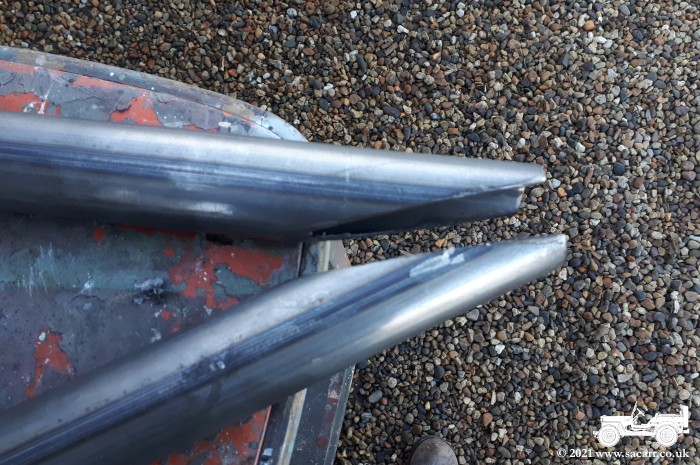 |
With that done, the crane head was jigged up between the two bars, using some G-clamps to set the height and some copper wire wrapped around the bars to hold them against the face of the crane
head. After a few tack welds, the A-Frame was lifted and propped up on a piece of wood to see how it looked. I was rather pleased with myself,
then occured to me there was nothing stopping me from rigging it up properly, so I went to the workshop and brought the winch and chain hoist back out. The winch was bolted in place and the cable strung to the A-Frame. It was winched up and the chain hoist hooked in place for some pictures. |
 |
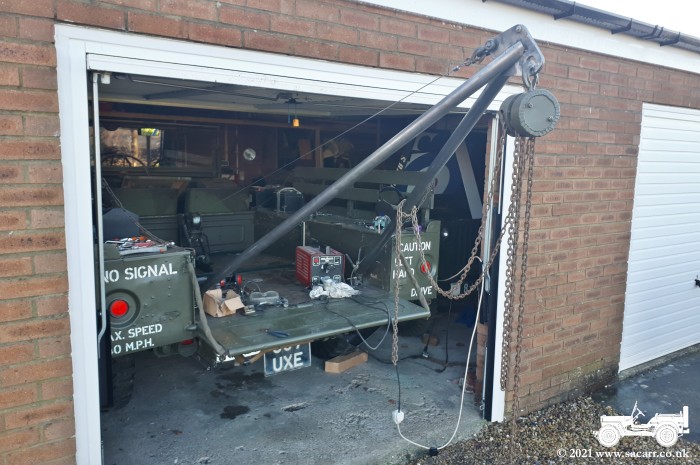 |
It was after 1pm and I was feeling hungry. I didn't want to leave it hanging unattended while I was still working on it, so lifted the A-Frame a bit higher, allowing me to close the tailgate to help support the crane while I was away. With the chain hook attached to the Dodge tow hook, I could probably drive around quite safely like this. I planned to weld some small hooks to the bars so the hoisting chain can be wrapped over them and secured.
Back from lunch and I welded up the hinge mounts fully and also the crane head. I used the tips from the tube offcuts to cap the ends of the tubes against the crane head to keep water out if it rains. When I bought the Dodge, it also had some shackles, plus a hook and pulley in one of the lockers. They were probably accessories from a WC52. So the crane was lowered and re-rigged with the hook and pulley at the top end of the crane, looping the winch wire back to the winch. This rigging halves the load on the winch and I think makes it look more interesting. |
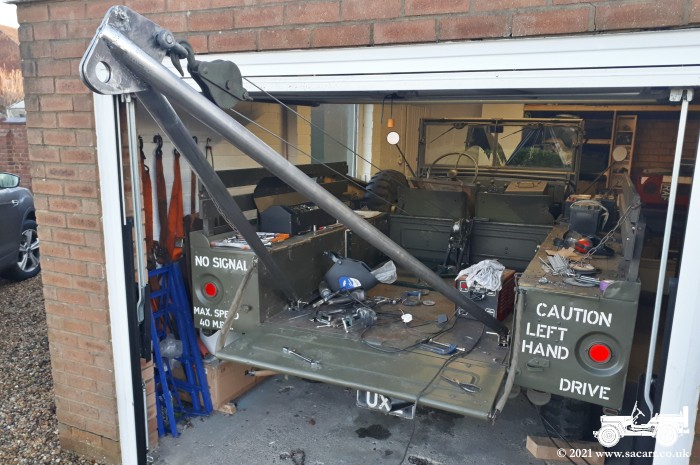 |
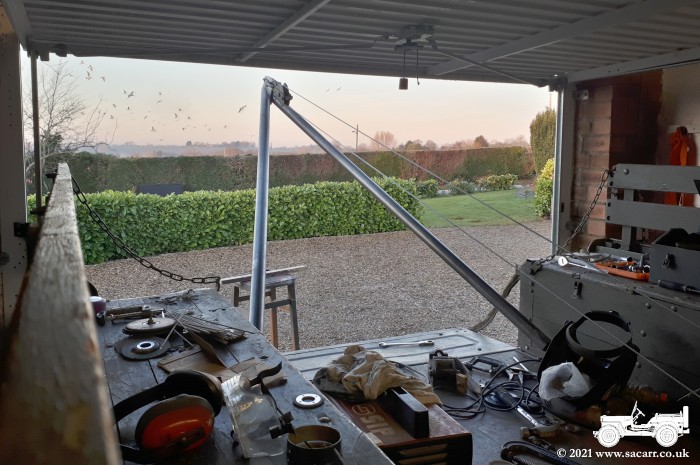 |
On
December 18th, I began some final fettling work. Another hole was drilled in the crane head for a second bolt to hold the two plates together. The welding distorted them slightly, so the additional bolt in the lower half helps to keep them together. Three hooks were welded to the right side A-Frame bar next. If I want to drive, I need to stop
the chains and hoist from swinging around. |
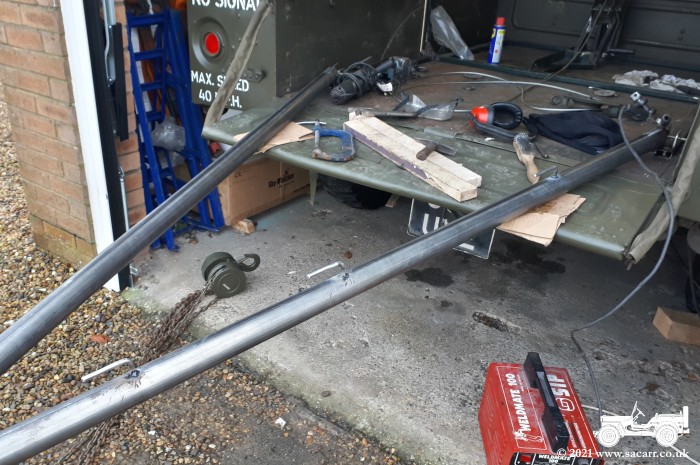 |
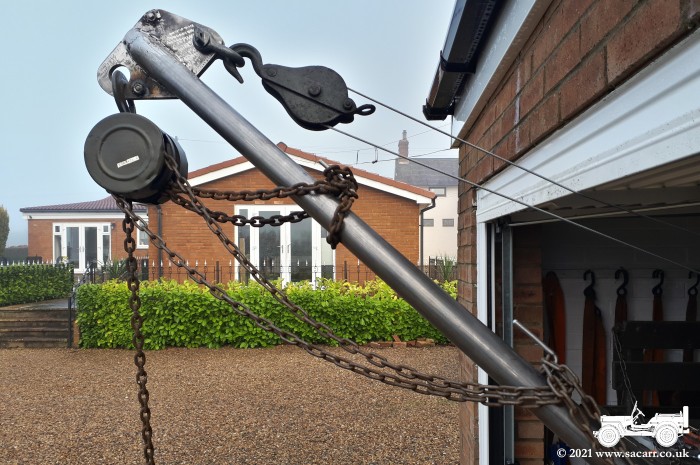 |
The hoist lifting hook is a good fit in the Dodge tow hook, so that can be fastened in there and the slack taken up against the pull of the winch cables. The hoist chains can then be wrapped around the A-Frame bars and over the hooks, keeping them out of the way.
Some heavier loads would be better lifted with the crane raised higher, putting more weight down
the A-Frame, rather than loading the winch cable. This would bring the load closer to the rear of the truck, but then the tailgate could be in the way of the
lift. With the pioneer rack fitted to the outside of the tailgate, it
wouldn't lower passed horizontal. |
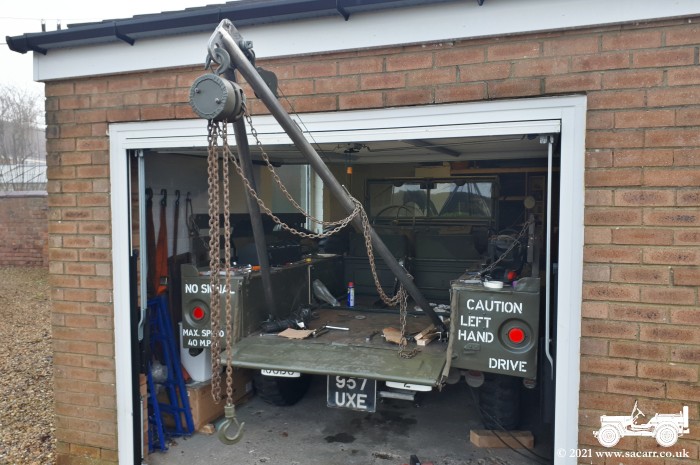 |
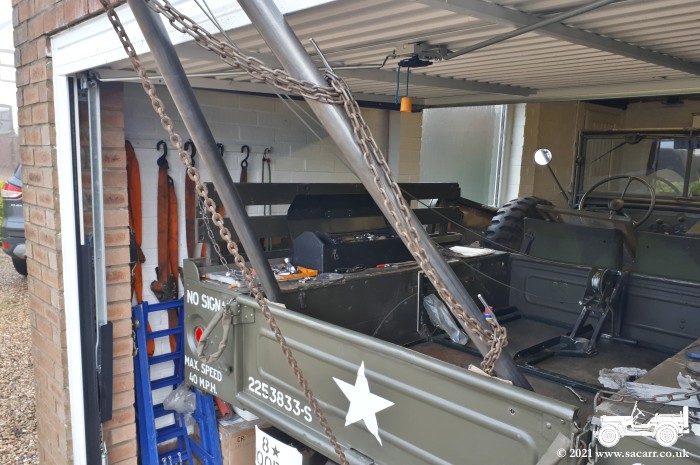 |
To allow the tailgate to fold down out of the way of any heavy lifts, the pioneer tool rack was removed. Now any heavy loads can be lifted near the back of the truck, passed the lowered tailgate. If the load can be lifted high enough, the tailgate could be raised beneath it, allowing it to be lowered onto the tailgate and pushed into the truck bed for transport. The tool rack will probably be mounted inside the truck, possibly on the bench seat back rest, next to the child seat. Before moving on, I did
a load test with me swinging from the crane.
OK, so it can manage 13 stone, plus boots, jeans, T-shirt, fleece and
hat so far!! |
 |
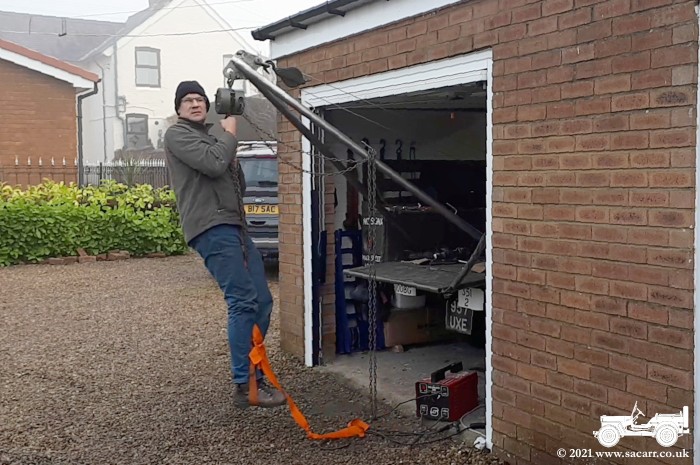 |
After that, I dismantled the crane and then removed the floor frame. With the frame out, I was able to finish the welding that couldn't be reached with the frame fitted in the truck. It was then taken into the workshop where a nut was welded into the hinge mount and a quick release bolt made for the hinge pin. It's now all ready for a final clean up and prime, followed by top coat painting. |
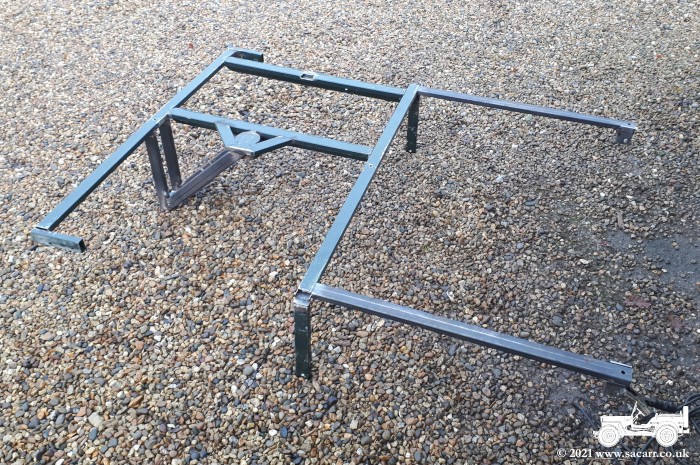 |
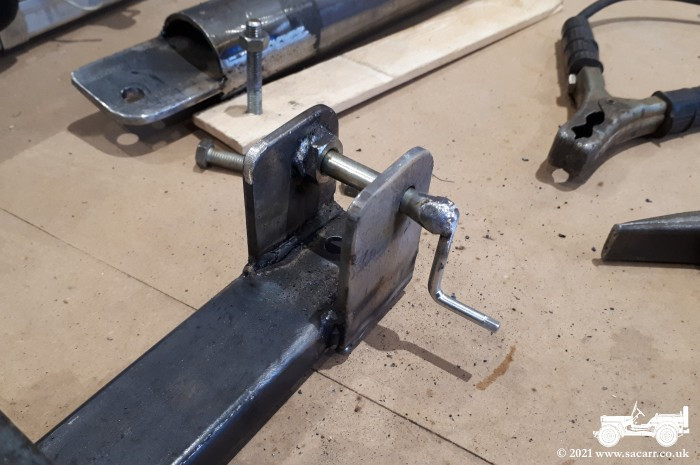 |
Sunday the 19th was a bit of an easier day with just a little welding and some painting. The two A-Frame bars were cleaned down with thinners and given a coat of red oxide primer. While they were left to one side, I welded some triangle reinforcing pieces to the uprights that support the winch, then added a loop for the pulley block to hook onto when not in use. |
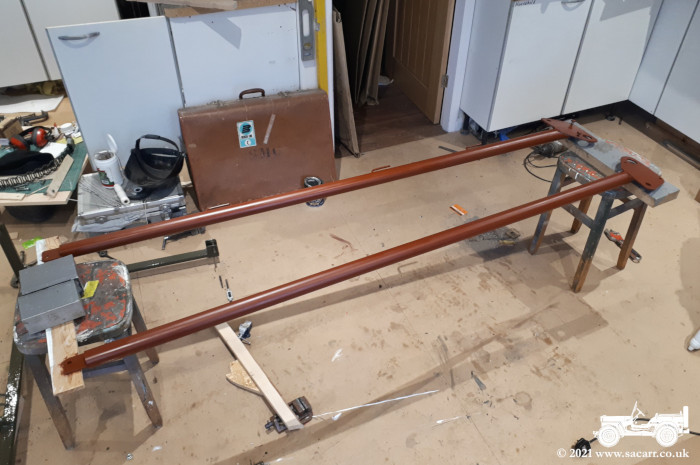 |
 |
The old observer's seat support tube needed trimming down a bit so that it wouldn't rub on the winch cable, but now that the pulley has somewhere to hook onto, it stops the cable unravelling from the reel. The original dull dark green floor frame paint was given a quick sand all over, then all the upper surfaces were painted in the same olive drab as the Dodge. That was as far as I could go until the first layers of paint
dried. The following day, the bars were painted olive drab and the
bottom of the floor frame. |
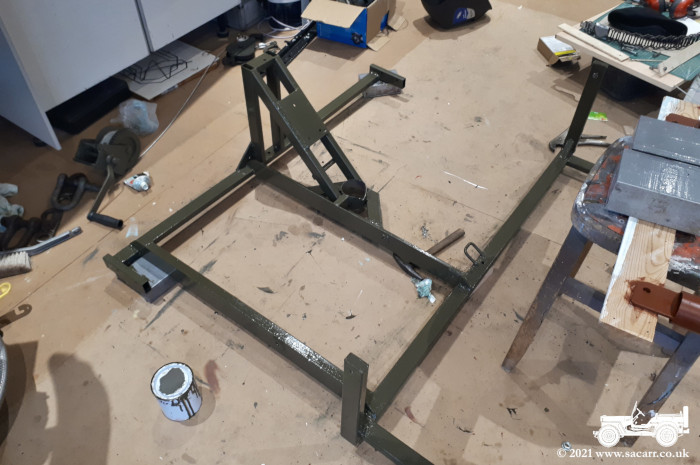 |
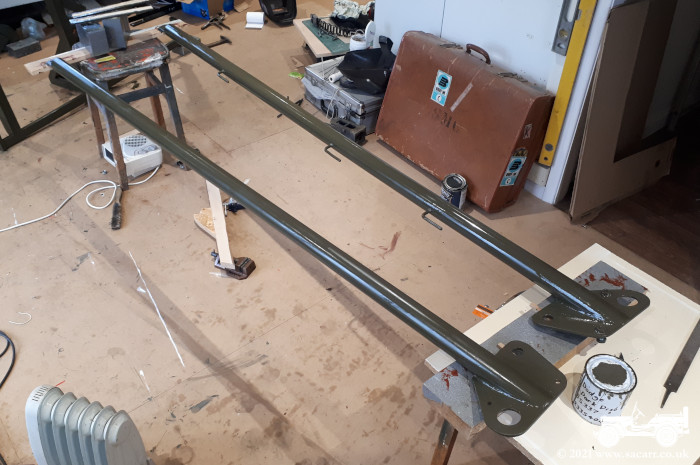 |
On
the 21st, the A-Frame bars received a second coat of olive drab
and were once again left to dry. The winch was mounted onto the floor frame and the handle painted with 'UP' and an arrow to avoid confussion.
Due to the gearing, the handle rotates the opposite direction to the reel. The reel was fully unwound too, as the inner crimped end was getting snagged on the cable as it wound onto the core of the reel.
To solve this, the inner crimped end was cable tied to the centre bar of the reel and taped over with duct tape to give a more even surface for the cable to wind onto. Approximately half of the 20 metre cable was carefully wound onto the reel and this was then given a couple of wrappings of duct tape. I don't need the full length of the cable anyway and this keeps at least half the reel from unravelling if there's no tension on the wire. The rest of the wire was then wound onto the reel, forming a nice even coil side to side as it was wound into place.
On the 22nd, the chain hoist was stencilled so I know which chain to
pull when lifting or lowering. It's actually a 1 tonne hoist, but wanting it to represent US wartime, I stencilled it slightly under rated at 2,000 pounds. |
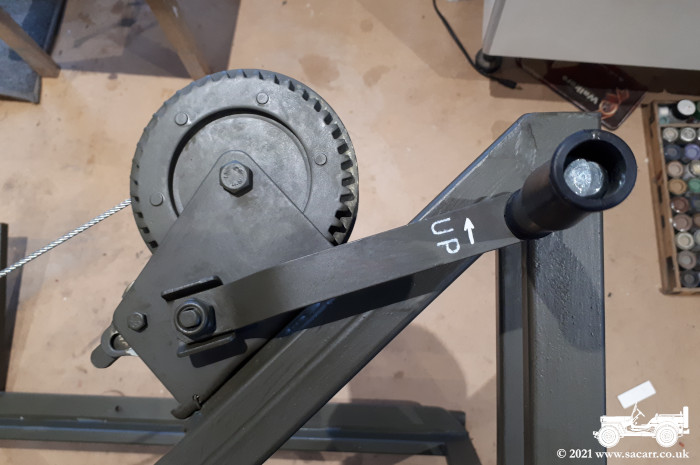 |
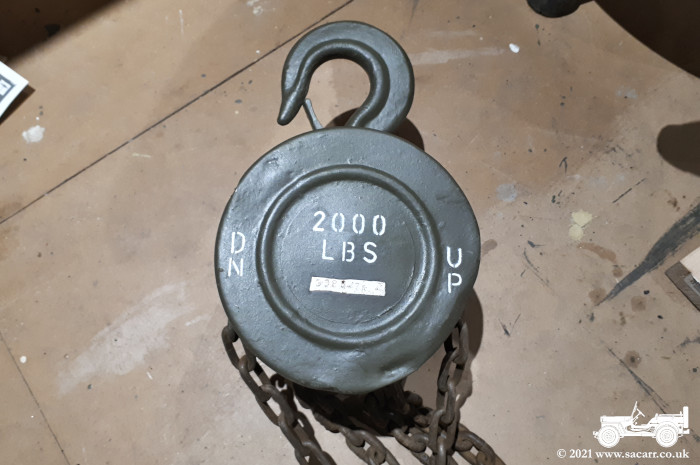 |
On the afternoon of the 23rd, the frame was carried back out to the Dodge for fitting. Most of the bolts were reused as they were, but a couple that went through the floor needed around a half inch trimming off. The wooden shims at the front fixings needed a little trimming, but everything went together without
problems. There's still plenty of cargo space for camping gear and
without all the radios and meteorological equipment it used to have,
there's more free bench space for passengers. |
 |
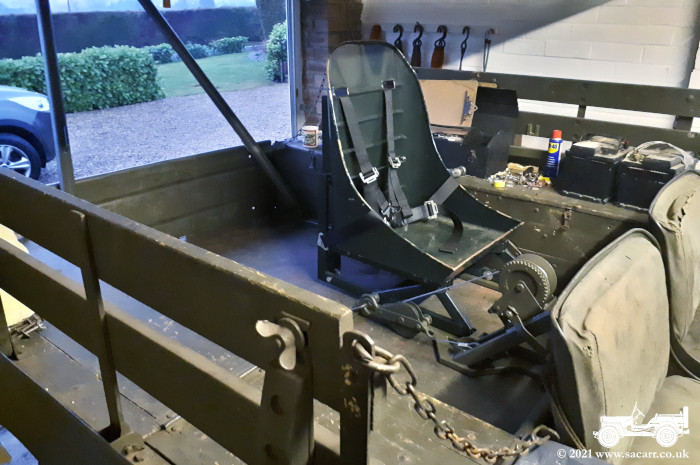 |
Once it was all fitted securely, I brought the A-Frame bars out and fitted those to establish the position of the wooden blocks I wanted to add. They were epoxied in place and left to set for a while.
Once the epoxy had cured sufficiently to hold the wooden blocks in place, the bars were de-rigged and taken back to the workshop where they were drilled for some self tapping screws. The screws were a little reluctant to cut through the 3mm steel, so a UNC thread was cut into the metal with a tap and that gave the screw the help it needed to start threading itself. With the screws in, both blocks were given a coat of olive drab,
with a second the next day. |
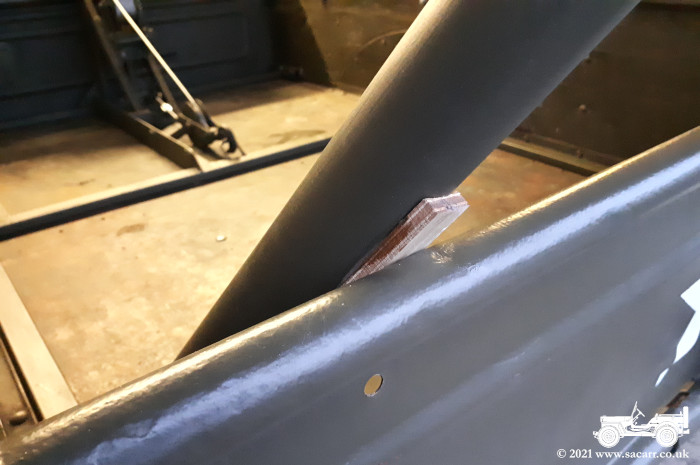 |
 |
While the epoxy
had been setting, my daughter's child seat was fitted back into the Dodge. It now sits much lower down than before, so she can see what's going on during a trip out and is probably further out of the draft from the cab roof. She currently still fits the modern child seat which fastens into this dummy B-17 pilot's seat, but before long, we're going to have to make a new padded seat and back rest. The four point harness is attached to the seat frame, as the modern seat relied on using the car seat belt. Before locking up the garage, all the
fixing bolts were given a coat of olive drab. |
While many
were winding down and relaxing, on Christmas eve I was still busy with the Dodge, pushing it towards completion for hopefully a trip out
before the year was done. Two hardwood rests were cut for the bars,
with half round notches for the bars to rest in. The Dodge won't fit
in the garage with the crane attached, so whether I drive with it
fitted or not, it still needs to be stowed to get the Dodge under
cover.
The rests
would be screwed to the locker lids but wouldn't prevent the lids from opening. With the rear rest mounted right at the back of the locker lid, it doesn't stop anyone from sitting on the bench seat if the crane is mounted rather than stored.
Once happy with the basic fit, the blocks were chamfered, painted and
left in my curing cabinet to bake the paint.
The crane head tucks in between the rest and the front of the truck bed. There's probably enough weight in them to keep them there, but if needed, I'll add something to hold them down.
|
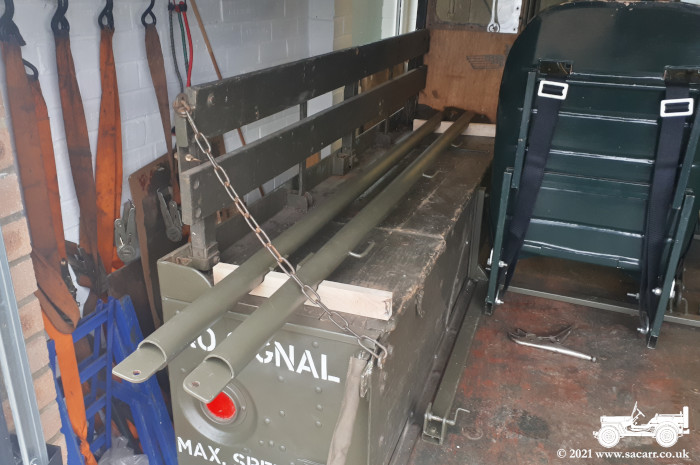 |
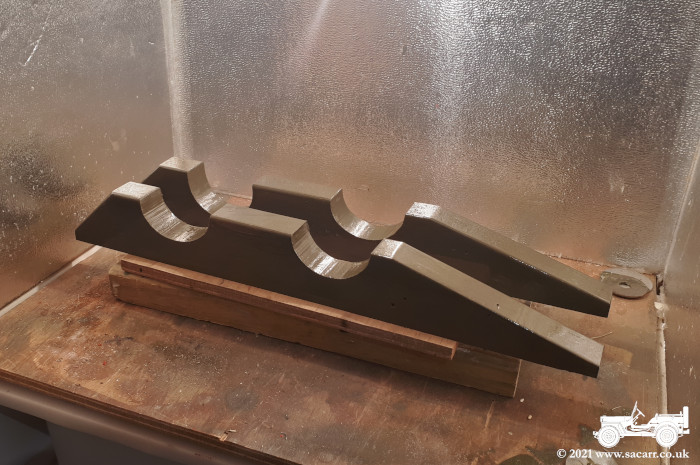 |
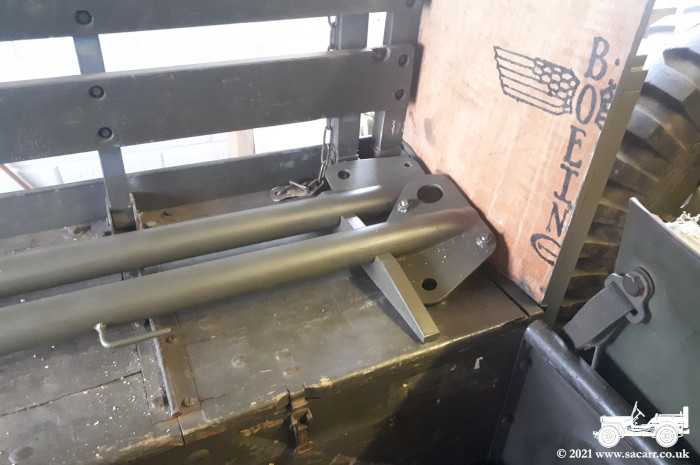 |
Last job on the crane was a quick ten minute task
on Christmas morning. There was a window of opportunity after present
opening and before the family arrived for dinner. Just two woodscrews
were needed in each bar support to hold them in place. Two small holes were drilled through the locker lid, countersunk on the rear. The bar rests were held in place and a pilot hole for the screws drilled through the lid and into the
rest.
Even with the bars in place, the rear locker can still be accessed if needed. I keep a few spares and fluids in that locker and will probably empty the rear right locker to keep the chain hoist and shackle in. They'll be easily accessible from that locker. I need to look for a shorter tool box which will probably go in the front left locker. The long tool box I had, used to live under the false floor along with the spare wheel. That is too long to fit in any of the lockers and I don't want it on show. |
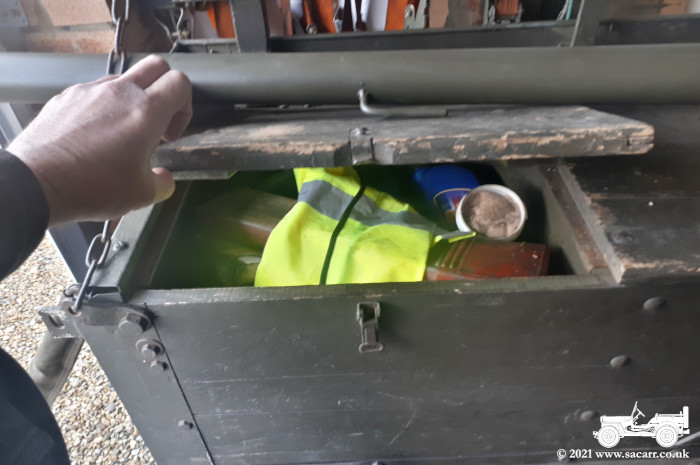 |
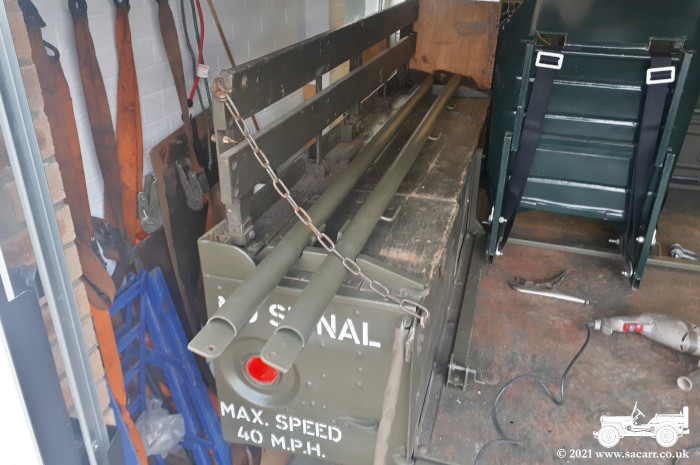 |
On
December 30th, Lynne, my daughter, a friend and myself took the Dodge
and M201 out for a local drive to get some photos of the finished
crane. I planned a fairly local route of around 14 miles, taking in a
number of lay-bys where we could pose for some shots with both
vehicles. |
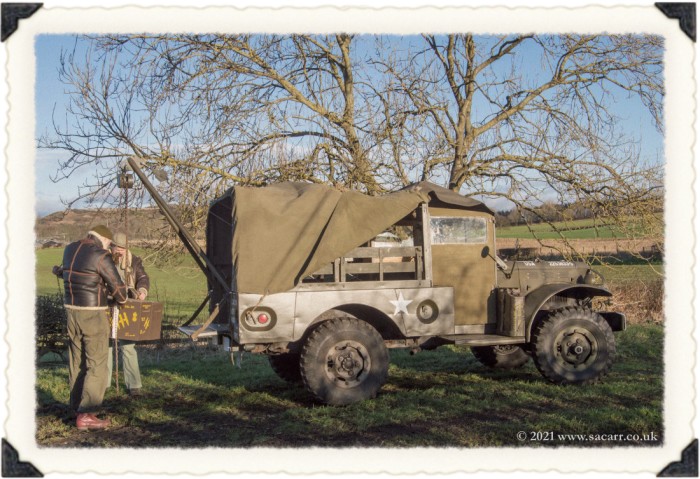 |
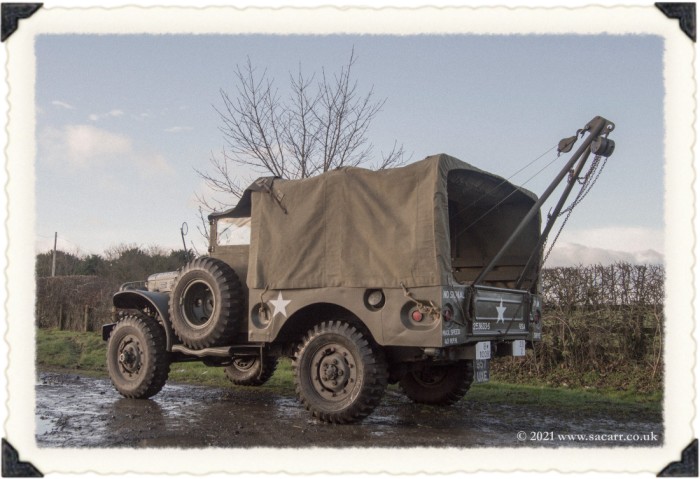 |
After
several days of rain, most of the remaining road salt should have been
washed away and the sky had a few clouds and plenty of sun; great for
photos. Lynne took most of the photos while Andy and I posed, both
with and without the crane in use. It should make a nice and different
talking point at shows. |
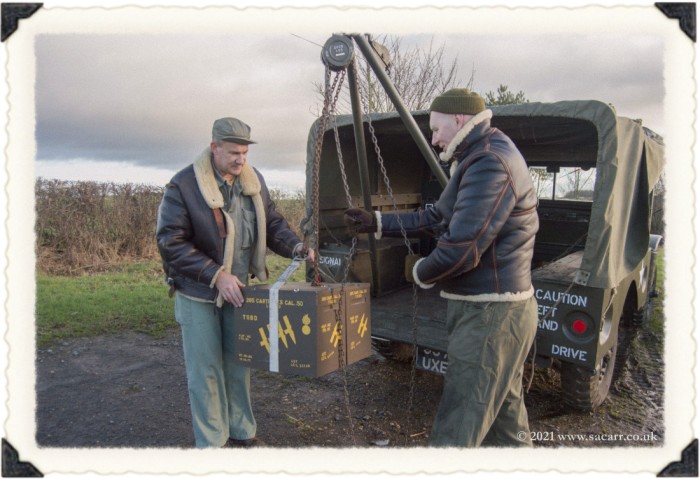 |
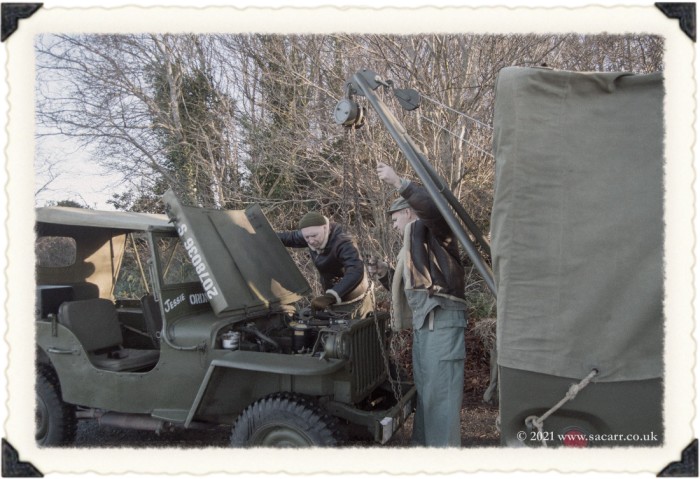 |
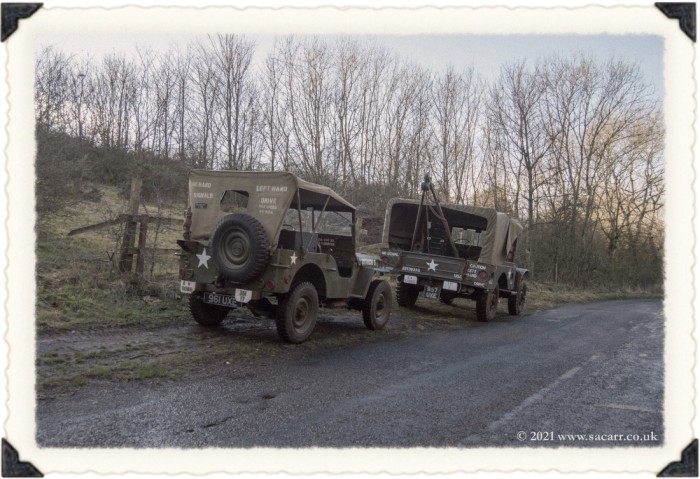 |
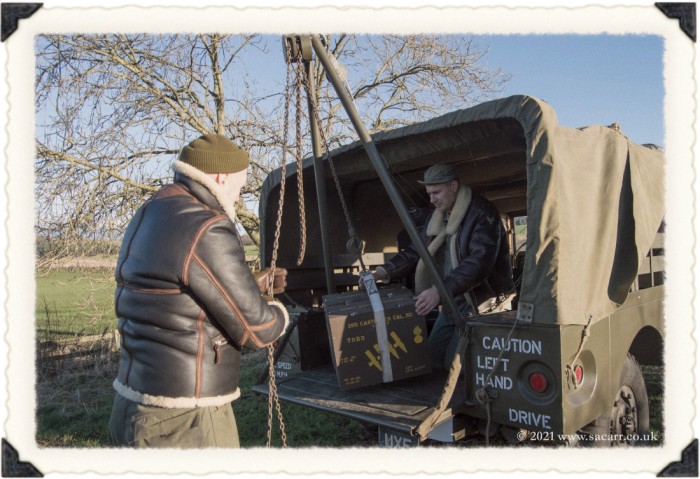 |
|
|